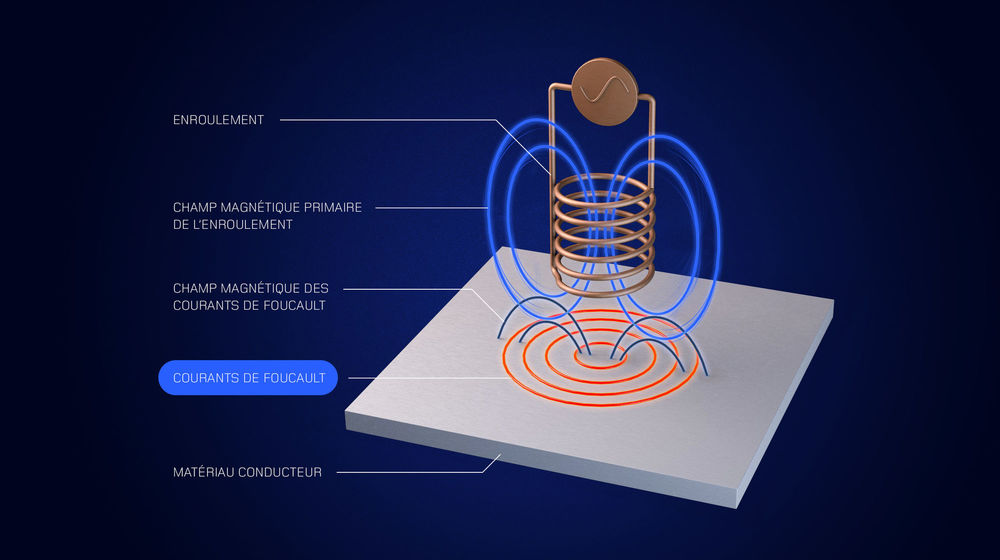
The technique harnesses a phenomenon known as electromagnetic induction, in which a magnetic field is generated by passing a current of variable intensity through a coil. On contact with a metal component, this field induces swirling "eddy" currents in the component. In accordance with Lentz's law, these eddy currents in turn emit a secondary magnetic field, opposing the field that initially created them. Any irregularities within the material (such as defects or fluctuations in electrical conductivity or magnetic permeability) disrupt the eddy currents' flow, influencing the secondary magnetic field and in turn altering the primary field inside the coil. A measuring instrument specially designed for ECT inspections detects variations in impedance, indicative of irregularities within the material. Eddy current testing is used across a broad spectrum of applications, which can be organised into the following categories: In-tube inspections using an internal probe; tube or bar inspections using a circling probe; surface probes; drilled hole probes; and special-purpose probes.
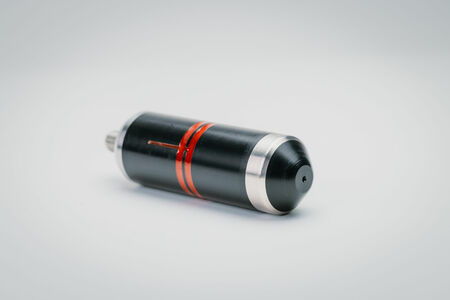
These probes are designed for inspecting straight tubes. This type of probe may feature a PEEK plastic/stainless steel protective ring or front and rear guides, to extend its service life. They can be fitted with centring cones for improved centring in the tube. These probes are available with a sheath or a clip-connector.
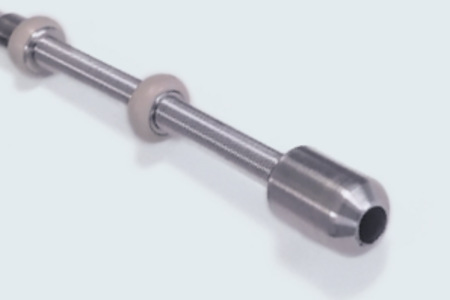
These probes are designed for inspecting formed tubes. The centring cones are made with high-tech plastics designed for optimal friction and wear resistance coefficients.
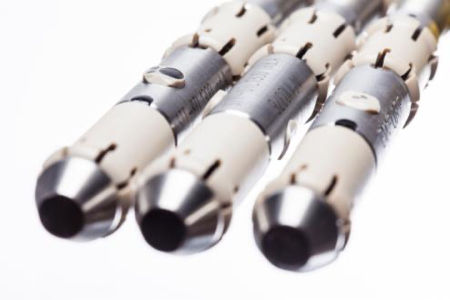
These probes move through tubes in a spiral motion, facilitating the detection and sizing of longitudinal or circumferential defects.
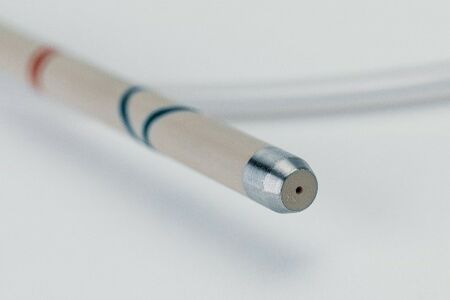
This probe allows for one-pass inspection of defects in all directions using two additional coils angled in the probe body in addition to the conventional axial coils. This probe model is available with several options depending on your application.
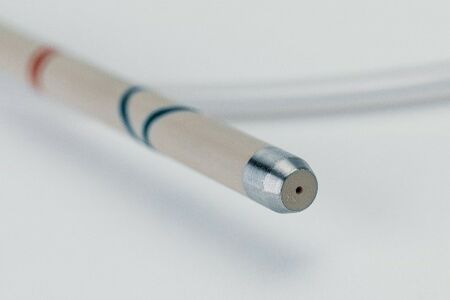
This probe allows for one-pass inspection of defects in all directions using two additional coils angled in the probe body in addition to the conventional axial coils. This probe model is available with several options depending on your application.
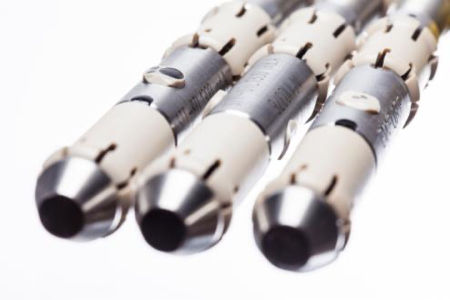
These probes move through tubes in a spiral motion, facilitating the detection and sizing of longitudinal or circumferential defects.
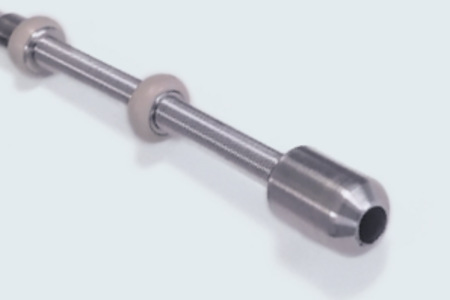
These probes are designed for inspecting formed tubes. The centring cones are made with high-tech plastics designed for optimal friction and wear resistance coefficients.
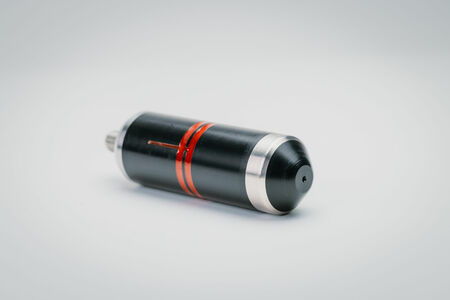
These probes are designed for inspecting straight tubes. This type of probe may feature a PEEK plastic/stainless steel protective ring or front and rear guides, to extend its service life. They can be fitted with centring cones for improved centring in the tube. These probes are available with a sheath or a clip-connector.